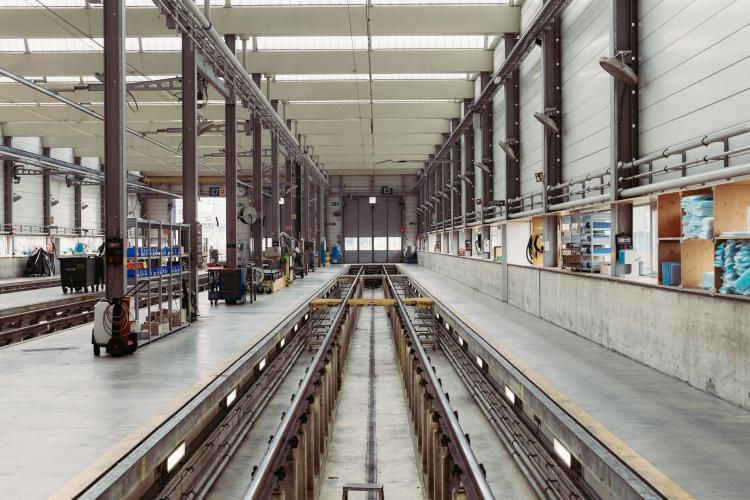
Over the last year, MEEA has participated in the Industrial Energy Efficiency Working Group coordinated by M-WERC, or the Mid-West Energy Research Consortium, a MEEA Member. Headquartered in Milwaukee, M-WERC is a unique thought leader, catalyst and incubator focused on the growth and economic competitiveness of the energy, power and control industry cluster across the Midwest. To guide this work, M-WERC develops Industry Roadmaps that pinpoint specific barriers to economic development in key areas. Their recently completed Energy Efficiency Industry Roadmap identified efficiency improvements in the industrial sector as a critical component of improving the competitiveness of Midwestern businesses.
M-WERC, in partnership with the Wisconsin Manufacturing Extension Partnership (WMEP), convened a working group to identify and develop solutions for the barriers to industrial energy efficiency (IEE). The vision for this group is to help the Midwest “become the nationally and internationally recognized leader for developing economically viable IEE projects, including low-water use, for small and medium sized manufacturers (<1,000kw per month), as measured by the number of projects developed, project conversion rate, and average energy savings in absolute and intensity based measures for projects developed.”
6 Barriers to Energy Efficiency Implementation
After several months of dialogue, MEEA, M-WERC and several other organizations including Leidos, Focus on Energy, We Energies, CBI, Milwaukee Area Technical College, Franklin Energy, the University of Wisconsin, WMEP, and the Wisconsin State Energy Office generated six themes representing the central barriers small- and medium-sized manufacturers face in implementing energy efficiency upgrades. They are briefly described below:
- Inadequate IEE Customer Support: A limited supply of industry sector, process specific, technical customer support expertise; most funding for EE programming in industrial sector goes to larger companies; inadequate support of Strategic Energy Management training for smaller companies
- Inadequate IEE Sales Skills and Efforts: Inadequate focus on driving the customer decision from the top down, with emphasis on overcoming key decision makers’ objections; economic evaluation methodologies are not always consistent with those used by customers; audit/assessment reports take too long and non-energy benefit streams are not fully identified or quantified
- Access to Customer Capital for Projects: IEE competes with limited capital required for core business investment; IEE projects frequently do not meet company’s required ROI; limited lower threshold, third party, attractively-priced financing opportunities
- Inadequate Development of New IEE Technologies, Products and Processes: Need increased focus on development and demonstration of specialized, industrial process-oriented technologies that cross multiple industry sectors; wider acceptance and support for waste heat capture or combined heat and power
- Inadequate Sized and Trained IEE Workforce: Suppliers need more trained assessors and installation technicians; customers need more internal energy experts or access to inexpensive, trusted, external advisers
- Lack of Trusted Third Party to Provide Impartial Guidance and Support to Customers/Consultants: Quality information on EE upgrades can be difficult to locate, especially when time is limited; customers depend too much on potentially biased vendors for information; need stronger, more objective, more numerous case studies on wide variety of industry subsectors; limited awareness of available resources, such as Industrial Assessment Centers, CHP TAPs, the Better Plants program, etc.
For more information on MEEA’s effort with this working group, please contact Mark Milby, MEEA Program Manager, at mmilby@mwalliance.org or (312) 784-7249.